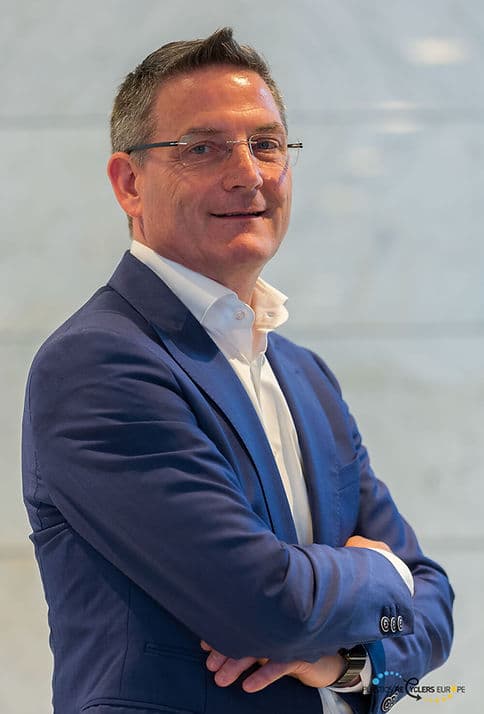
Who we are
Plastics Recyclers Europe (PRE) is an organisation representing the voice of the European plastics recyclers who reprocess plastic waste into high-quality material destined for the production of new articles. Recyclers are important facilitators of the circularity of plastics and the transition towards the circular economy.
Plastics recycling in Europe is a rapidly growing industry representing over €9.1 billion in turnover, 13.2 million tonnes of installed recycling capacity, around 850 recycling facilities and over 30.000 employees.
850 RECYCLING
FACILITIES
13.2 MILLION TONNES
INSTALLED CAPACITY
€9.1 BILLION
TURNOVER
30,000
EMPLOYEES
WHAT DO WE
STAND FOR
- Advancing circularity of plastics through
increased quality plastics recycling & use
of recycled materials in high-end products - Improving recyclability of plastic products
- Harmonising of the recycling standards &
practices across Europe - Genuine transition towards the circular
economy
MAKING
PLASTICS
CIRCULAR
PRE Board
Representatives are elected by the PRE General Assembly.
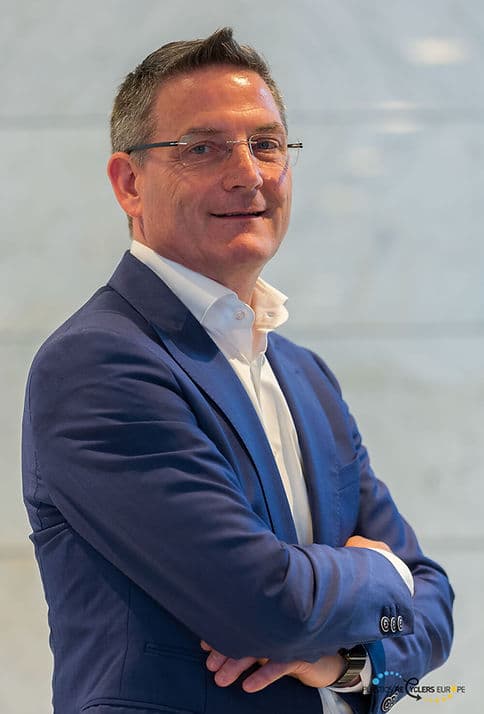
Ton
President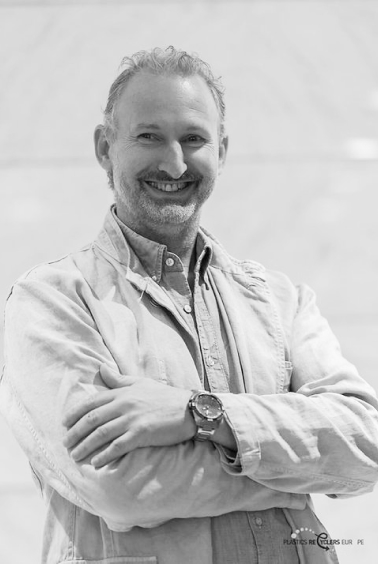
Casper
van den Dungen
Vice President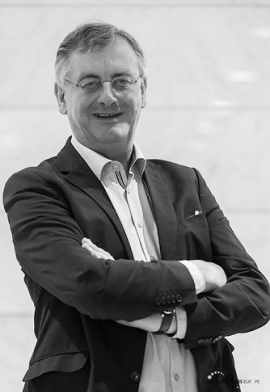
Jim Armstrong
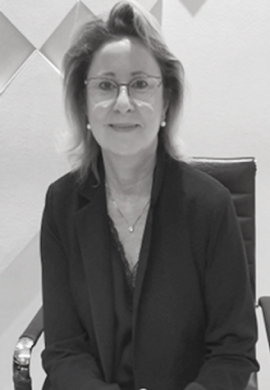
Maribel Cansell
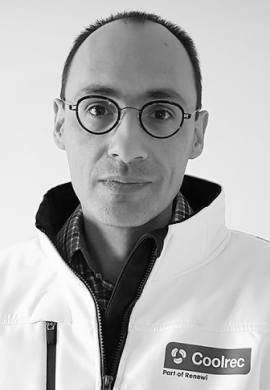
Tom Caris
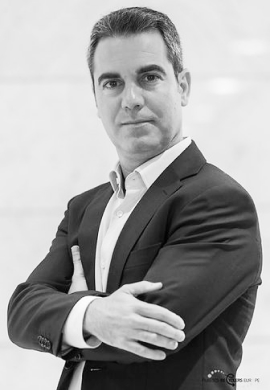
David Eslava
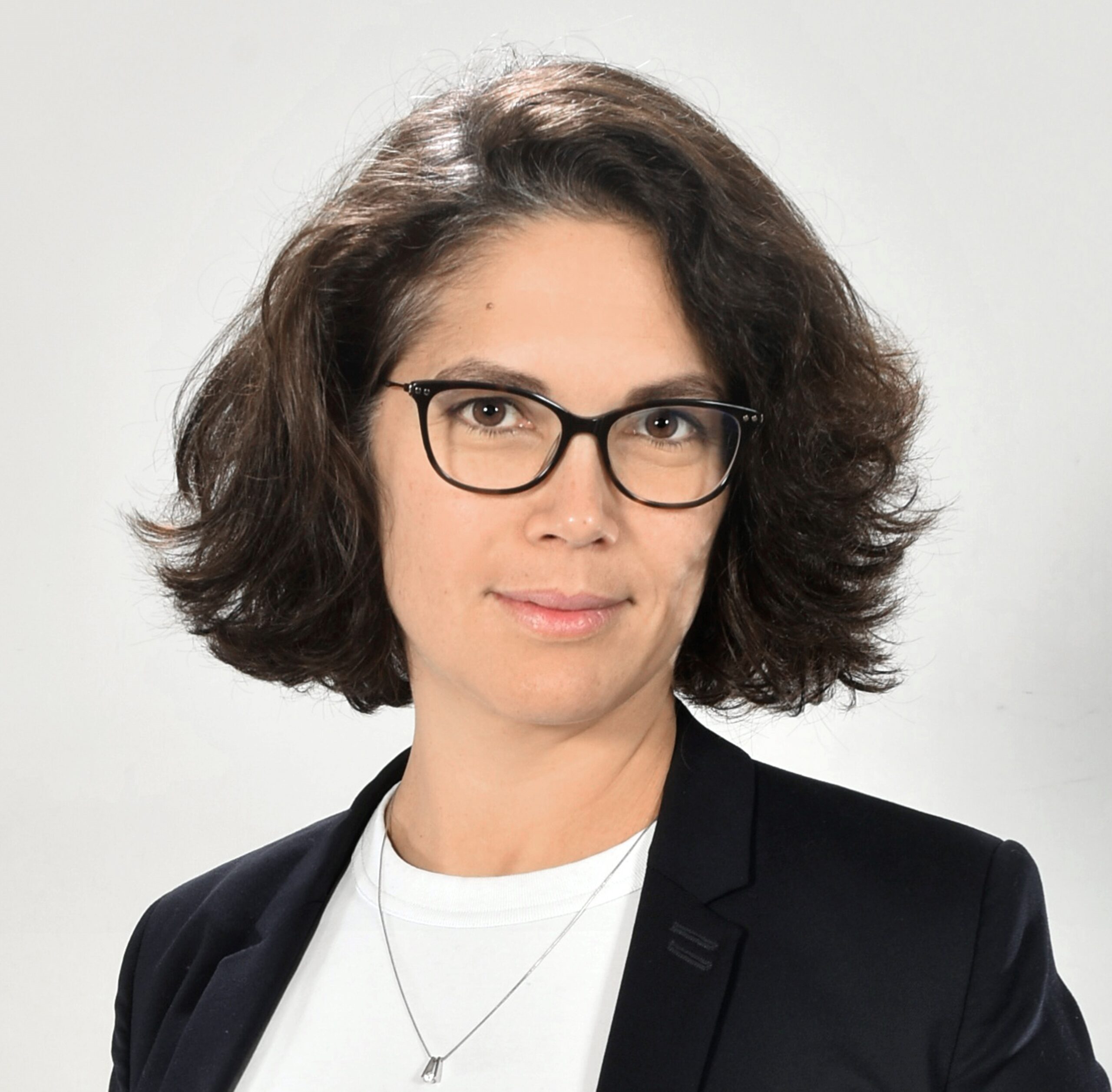
Sophie Sicard
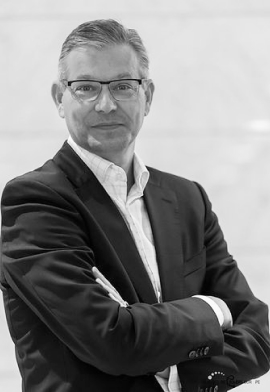
Herbert Snell

Paolo Glerean

Rune Thoralfsson
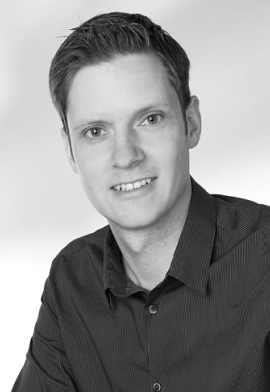
Andreas Witschnigg
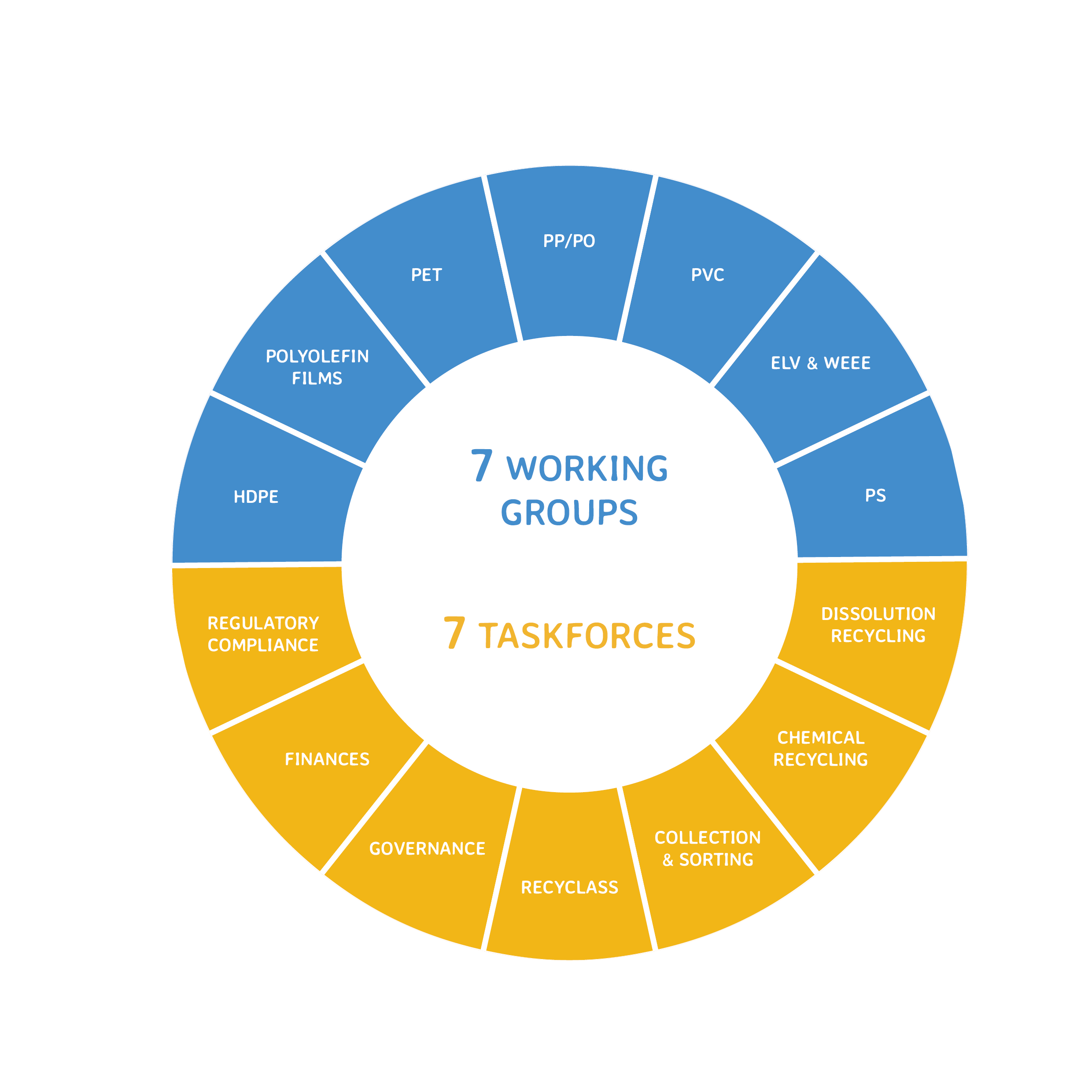
WORKING
GROUPS
7 Working Groups and 7 Taskforces represent the interests of different industry segments while coordinating activities and general objectives of PRE.
Working Groups look for solutions that can help advance recycling and promote the best practices while ultimately seeking to increase quality collection, sorting, recycling and increased use of recycled plastic in Europe.
STAKEHOLDERS
COLLABORATIONS
The involvement of the entire value chain is key in advancing plastics circularity. With that in mind, PRE collaborates with important industry players.
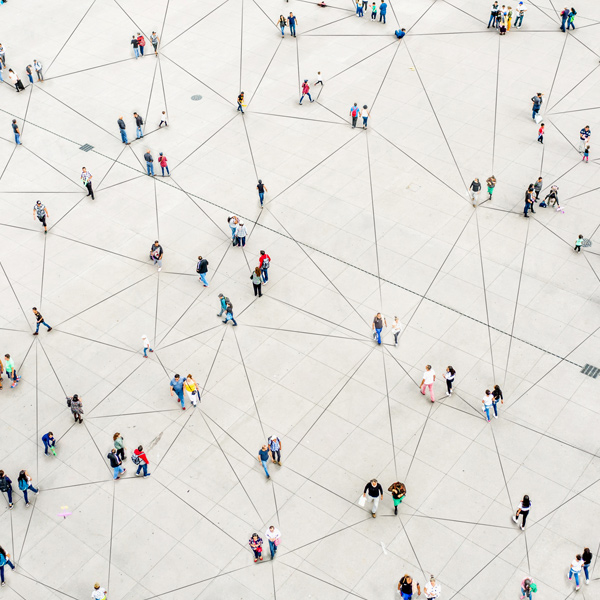
Making Plastics Circular
PRE works toward making plastic circular via a holistic approach.